In an enormous step in direction of the way forward for energy technology and propulsion, a crew led by Affiliate Professor Beni Cukurel at Technion – Israel Institute of Know-how, has designed a micro fuel turbine utilizing additive manufacturing (AM), also referred to as 3D printing. This revolutionary growth presents an ingenious strategy in direction of the ‘Design for Additive Manufacturing’ precept, considerably difficult typical manufacturing paradigms.
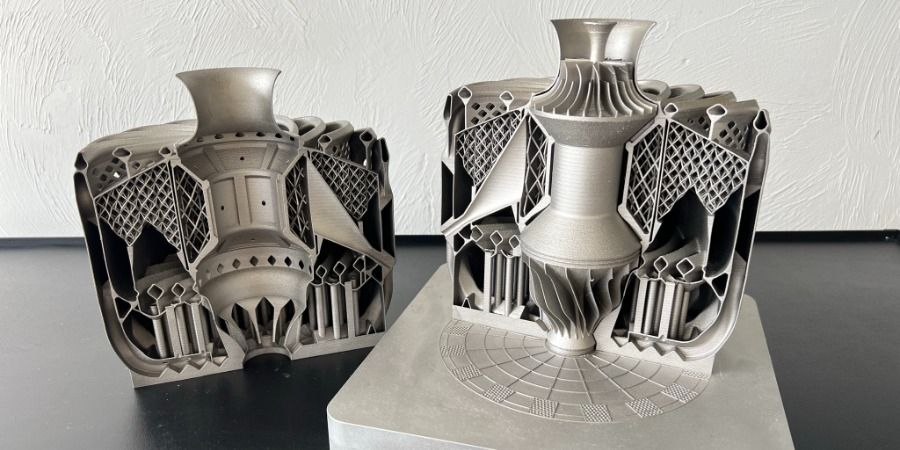
Not like typical manufacturing methods, Cukurel’s crew and the Turbomachinery and Warmth Switch laboratory tapped into the potential of AM in its purest type. In his phrases, “If you’re utilizing [AM] simply as one other manufacturing approach, you’re probably not absolutely capitalizing on the advantages of additive manufacturing.” Slightly than merely integrating AM in its place device, the crew reimagined it as a core useful resource, creating designs a priori to fulfill constraints and leverage the advantages of AM.
On the coronary heart of their analysis are micro fuel generators, designed for proportionate energy technology. Cukurel defines micro fuel generators as techniques able to producing electrical energy under 300 kilowatts and thrust under two kilonewtons. Taking the AM strategy, the crew began their first venture, a 5cm scale micro fuel turbine that would doubtlessly present 300 watts for a drone. The micro turbine affords a big enhance in flight time as a result of its larger vitality density in comparison with typical batteries.
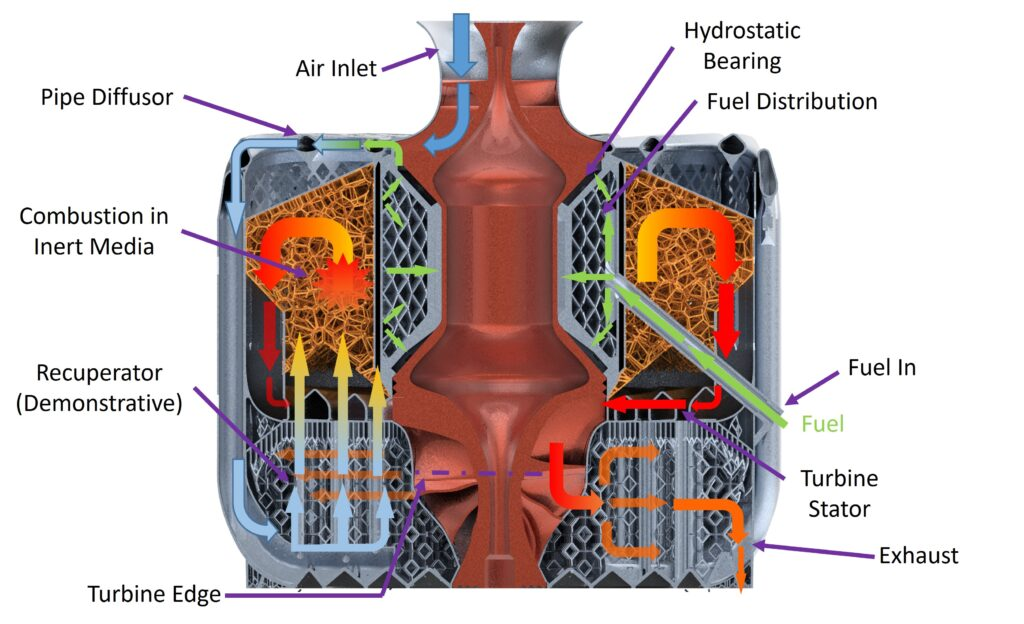
The crew didn’t cease on the micro fuel turbine; they additional leveraged their AM data through the COVID-19 disaster. They innovated a pre-assembled, self-supported turbomachinery design for medical ventilators. “We transitioned this know-how that we developed in pre-assembled self-supported turbomachinery architectures to fuel generators,” stated Cukurel.
The breakthrough provided by these pre-assembled, self-supporting micro fuel generators hinges on their on-demand availability and cost-effectiveness. The first value is confined to machine time and energy consumption, significantly lowering manufacturing expenditure.
Cukurel acknowledged that such revolutionary work was solely attainable as a result of a fruitful collaboration with von Karman Institute for Fluid Dynamics, Izmir Katip Celebi College, and PTC. The NATO-funded venture noticed every get together carry its distinctive experience to the desk. Von Karman Institute supplied high-fidelity simulation for aerodynamics and combustion, Izmir Katip Celebi College lent its computational fluid dynamics expertise for assessing the load-bearing capability of hydrostatic bearings, and PTC provided its intensive data in AM applied sciences, specifically by its highly effective CAD design and simulation framework, Creo.
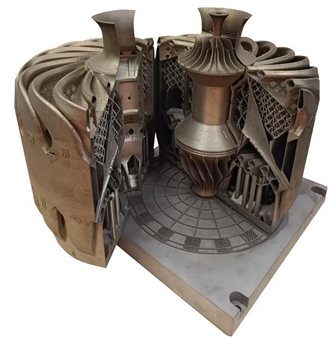
Optimizing efficiency with additive manufacturing
Addressing the constraints of design for additive manufacturing, Cukurel explains that they started by creating a diminished order mannequin. In easy phrases, that is an optimized mannequin that maintains the essential points of the unique system, however simplifies it for simpler evaluation and use.
In designing a jet engine, historically, aerodynamics takes heart stage. The aim is to realize peak efficiency when it comes to thermodynamics, translating to the thrust-to-weight ratio and particular gas consumption, or in different phrases, energy and vitality density. Nevertheless, this strategy falters on the subject of miniaturized engines.
“What we’ve created are diminished order fashions that seize all of the disciplines current within the engine. These embody aerodynamics, warmth switch, rotor dynamics, and combustion, amongst others,” Cukurel explains. Consider it like condensing a symphony right into a solo efficiency – it is advisable keep the essence of the piece whereas additionally accommodating the capabilities of the lone performer.
He continues to element how they’ve created a multidisciplinary optimization surroundings {that a} priori is aware of all of the constraints of additive manufacturing. This mainly means they’ve designed a system that, from the start, understands the bounds of what it will probably create. It’s like an skilled architect who is aware of to not design a roof with angles too steep for the constructing supplies to assist.
They’ve ensured that each layer constructed through the manufacturing course of is self-supported whereas obeying the constraints of additive manufacturing, which incorporates issues for cantilever angles, minimal thicknesses, and porosity, amongst others.
When requested in regards to the materials used within the part being mentioned, Cukurel confirms that it’s a metallic half printed with an EOS M 290. “We’re additionally utilizing Lithoz for all our ceramic manufacturing,” he provides. Lithoz is a ceramic manufacturing firm that Cukurel speaks extremely of, stating that they’ve been “very supportive and passionate about this distinctive software of the know-how.”
Ceramic elements, whereas being more durable to fabricate, provide benefits like smaller defect sizes and smoother finishes, resulting in improved aerodynamic efficiency. This efficiency interprets into vital financial savings in gas consumption, therefore the potential attraction of utilizing ceramics for particular elements.
Cukurel concludes by emphasizing the significance of hitting the conceptual design goal, noting {that a} deviation of as little as 5% can affect gas financial savings or thrust by virtually the identical margin. On the earth of jet engine design, even the smallest share factors can result in main modifications. The compressor efficiency of the ceramic elements was aerodynamically someplace between three to 4 share factors better, “I do know it sounds small, however folks sacrifice their firstborn youngster for the 1% distinction in efficiency,” stated Cukurel.
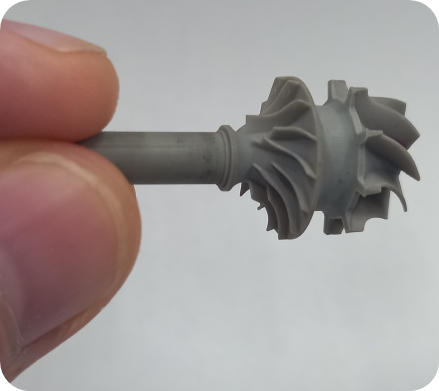
Is the way forward for vitality 3D printed?
The way forward for vitality may very well be reinvented by Israeli researchers and their work on preassembled engines utilizing 3D printing know-how. Their venture, specializing in the appliance of micro fuel generators in distributed vitality technology, is shaking up typical understandings of vitality effectivity and creating new potentialities for sustainability.
Cukurel provided two distinct functions for the know-how. Firstly, he highlighted army utilization, particularly unmanned aerial techniques. On this sphere, provide chain disruption is a big concern, doubtlessly leaving essential operations with out important elements like bearings for six to 9 months. The preassembled engine know-how circumvents this downside by eliminating the necessity for such a provide chain altogether.
The second, and arguably extra compelling software, is in distributed vitality technology. The standard centralized energy crops have an vitality effectivity cap at round 65%, that means 35% of vitality generated merely goes to waste. Cukurel proposed an answer utilizing mixed warmth and energy with distributed micro fuel generators in localities.
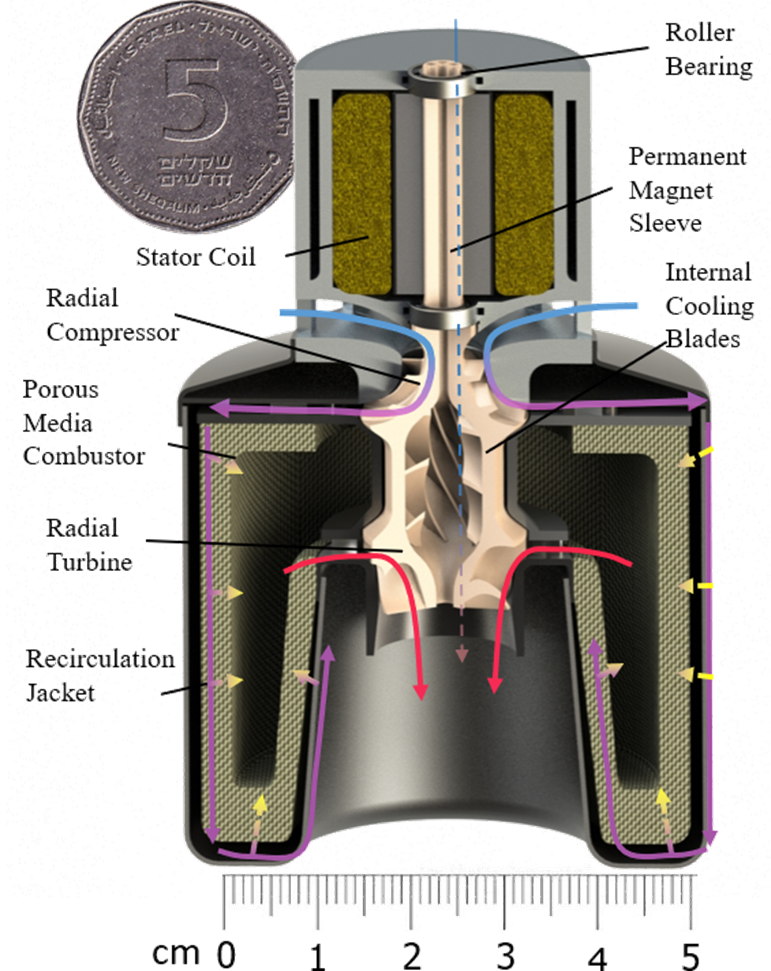
He additional defined, “Renewables are interrupted sources. You don’t wish to depend on whether or not there can be wind right now, proper? Or there’ll be solar right now. You wish to run your manufacturing unit it doesn’t matter what. So then how do you’ve gotten an agile, strong grid even when your renewables could or is probably not producing?”
Agile on this context doesn’t imply sprinting round a observe. It refers back to the capability to rapidly adapt and reply to modifications in vitality demand. On this case, these modifications are the unpredictable outputs of renewable vitality sources. Conventional centralized energy crops aren’t precisely Usain Bolt on this race—they’re not constructed for fast modifications. Small micro fuel generators, nonetheless, are.
Though the transformative potential of this know-how is obvious, a serious impediment lies within the return on funding. Because it stands, the price of these micro fuel generators is simply too excessive to yield a passable ROI in an inexpensive timeframe. But, the know-how mentioned right here affords a possible breakthrough by drastically lowering the related prices.
Moreover, these researchers have plans to commercialize their work. A by-product from Technion is within the pipeline, and partnerships with trade gamers and strategic traders are on the playing cards. Cukurel expressed his pleasure on the potential societal affect of their work, notably in enabling micro fuel generators to burn ammonia, which might act as a renewable, inexperienced, carbon-free gas. He passionately defined, “Overlook about all this work that I’ve talked about to you. Okay, simply to have the ability to have a micro fuel turbine that’s burning ammonia, when it comes to sustainability is a breakthrough.”
Ammonia has been used as gas earlier than, notably throughout World Conflict II in Belgium, however the combustor designs for fuel generators have modified considerably since then. The know-how Cukurel and his crew have developed — a porous media combustor — is especially fitted to burning ammonia. Whereas they didn’t invent the porous media combustor, they’re the primary to use it to this panorama.
With my curiosity sufficiently piqued, I delved additional into the mechanics of ammonia combustion.

Sustainable vitality utilizing ammonia engines
The wartime ammonia-powered engines offered plenty of challenges, primarily their sensitivity to gas and a normal lack of flexibility. That’s why Cukurel and his crew discovered fuel generators a extra applicable know-how for his or her venture.
“In fuel generators,” Cukurel defined, “many of the combustor designs use a totally completely different know-how. They optimize for vaporization, then have these dilution tubes to meter the gas, and introduce the new gases into the turbine.” What units the Technion crew aside is their distinctive software of a selected know-how – the porous media combustor. That is the primary time it’s been utilized to ammonia-burning micro fuel generators, making their work ground-breaking.
Let’s demystify the time period ‘porous media combustor.’ It’s a particular sort of combustor the place the fuel-air combination is burned inside a porous medium, creating extremely environment friendly, low-emission combustion. This isn’t one thing new; it has been round for at the least 50 years, with conventional manufacturing strategies involving dipping foams right into a ceramic slurry after which sintering them. Nevertheless, as Cukurel factors out, this offers you “no management over the porosity and the way it will get distributed within the move path.”
The breakthrough lies within the software of additive manufacturing. I used to be lucky sufficient to look at considered one of these combustors, and what caught my eye was its doughnut form with an natural, bubble-like lattice construction inside. The porosity of this construction modifications within the move path, which on this case is radially inward. That is the place the utility of 3D printing is available in, because it permits for management of the porosity gradient that’s unattainable to realize with conventional manufacturing methods.
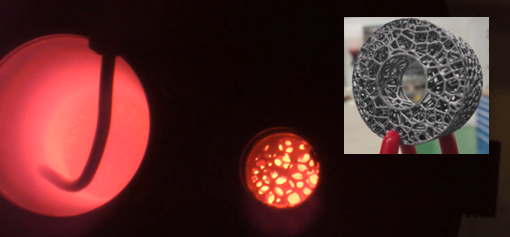
Cukurel can also be a co-author of a current paper offering a complete evaluation of the design, manufacturing, meeting, and high-speed testing of monolithic rotors utilizing Lithography-based ceramic manufacturing (LCM) and Selective Laser Melting (SLM) methods. Entitled, Ceramic and metallic additive manufacturing of monolithic rotors from sialon and Inconel and comparability of aerodynamic efficiency for 300W scale microturbines, that is the primary research to instantly evaluate micro-turbomachinery elements made with these strategies utilizing aerodynamic and manufacturing high quality assurance diagnostics. The paper examines the aerodynamic implications of support-free compressor and turbine design, formulates detailed manufacturing issues and course of parameters for each LCM and SLM, and conducts high quality evaluation of the elements by floor and CT scans, in addition to SEM micrography. The outcomes reveal that LCM rotors exhibit larger geometric element, higher floor end, fewer manufacturing-related floor artifacts, and decrease porosity in comparison with SLM rotors.
These groundbreaking ideas and future functions might change the world as we all know it. As we face the existential risk of local weather change, improvements like these should not simply intriguing; they could be essential for our survival.
Learn extra in our Interview sequence right here:
Peter Hansford, CRO at Wayland Additive, fixing a 20-year downside
Alloy Enterprises CEO Ali Forsyth, metallic additive manufacturing and disruption
Katie Snediker, CEO Jett3D, discovering a worthwhile area of interest in 3D printing
Paul Powers, founding father of Thangs and Physna, on remodeling the 3D design file-sharing market
Nadav Goshen, CEO of UltiMaker on Thingiverse, AI instruments and a message to the 3D printing group
What does the way forward for 3D printing maintain?
What engineering challenges have to be tackled within the additive manufacturing sector within the coming decade?
To remain updated with the newest 3D printing information, don’t neglect to subscribe to the 3D Printing Business e-newsletter or observe us on Twitter, or like our web page on Fb.
When you’re right here, why not subscribe to our Youtube channel? That includes dialogue, debriefs, video shorts, and webinar replays.Are you searching for a job within the additive manufacturing trade? Go to 3D Printing Jobs for a collection of roles within the trade.
The initiatives talked about above have been supported as follows:
5 cm scale extremely micro fuel turbine (UMGT)
The exercise has been funded by US Military Analysis Laboratory
Additive Manufactured Pre-Assembled Micro-Turbojet Engine (APE)
The Turbomachinery and Warmth Switch Laboratory of Technion-Israel Institute of Know-how has been main the multi-disciplinary turbomachinery design course of in collaboration with PTC, von Karman Institute for Fluid Dynamics and Izmir Katip Celebi College. The exercise has been funded partly by the NATO-Science for Peace and Safety Program.
The analysis concepts have been realized in digital modeling and simulation-led design of the complete engine topology in Creo, a PTC Know-how CAD software program. Moreover, EOS Methods helped to finish the digital thread by implementing the environment friendly course of for additive manufacturing. Utilizing Inconel 718 powder, the ultimate geometric proof of idea demonstrators have been printed by The Israel Institute of Supplies Manufacturing Applied sciences, affiliated with Technion’s Analysis and Growth Basis, on EOS M290 and by EOS Methods on EOS M300 printers.
Porous Media Combustion of Ammonia
Collaboration with Asst. Prof. Joe Lefkowitz
The exercise has been funded by the Israel Ministry of Power
Featured picture reveals Geometric Know-how Demonstrator of Additively Manufactured Pre-Assembled Micro-Turbojet Engine. Picture by way of Technion Turbomachinery and Warmth Switch laboratory.