Tesla (Nasdaq: TSLA) is making an attempt to grasp the artwork of casting giant, complicated automobile elements in a single go. If it succeeds, it should change how automobiles are made, making it quicker and cheaper to provide electrical automobiles (EVs). In keeping with a Reuters report, 5 individuals acquainted with Tesla’s plans revealed that the corporate goals to revolutionize the normal, sophisticated, time-consuming, and costly course of of making giant elements like a automobile’s underbody, which generally requires assembling quite a few smaller items.
To beat these challenges, Tesla is wanting into 3D printed sand molds, that are less expensive and faster to make than conventional steel molds. This fashion, they will check new designs with out spending a ton of cash. Reuters sources revealed that the carmaker can be experimenting with particular forms of steel that work properly for these huge, one-piece castings. The aim is to hurry up how automobiles are made and make electrical automobiles extra inexpensive.
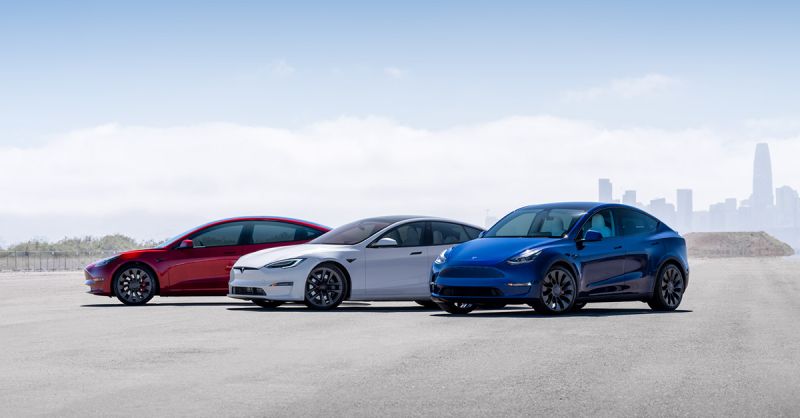
Progressive casting
In keeping with insiders who spoke to Reuters, this seemingly easy shift in materials alternative might be a game-changer for the whole business. Conventional molds constituted of steel are costly and time-consuming to change. For instance, a dashboard mould alone can value between $100,000 to $150,000, whereas a mould for a bumper may vary from $50,000 to $100,000. Engine part molds can begin at round $20,000 and go as much as $80,000 or extra, relying on the complexity and materials.
A single tweak within the design of those molds may value as a lot as $100,000. However in relation to creating a wholly new mould from scratch, the prices can soar as much as $1.5 million, particularly for big, complicated buildings like a automobile’s underbody. A sky-high determine like this accounts for detailed design work, specialised equipment and labor, rigorous testing to fulfill high quality and security requirements, and the price of sturdy supplies required for casting. Such excessive prices make Tesla’s exploration of 3D printed sand molds a probably revolutionary growth within the automotive manufacturing business.
In distinction, 3D printed sand molds provide a much more versatile and cost-effective resolution. Engineers can simply revise designs utilizing a digital design file and 3D printers, and a brand new sand mould may be printed inside hours at a fraction of the price. This dramatically shortens the design validation cycle from so long as a 12 months to simply two to a few months, permitting for extra fast innovation and changes.
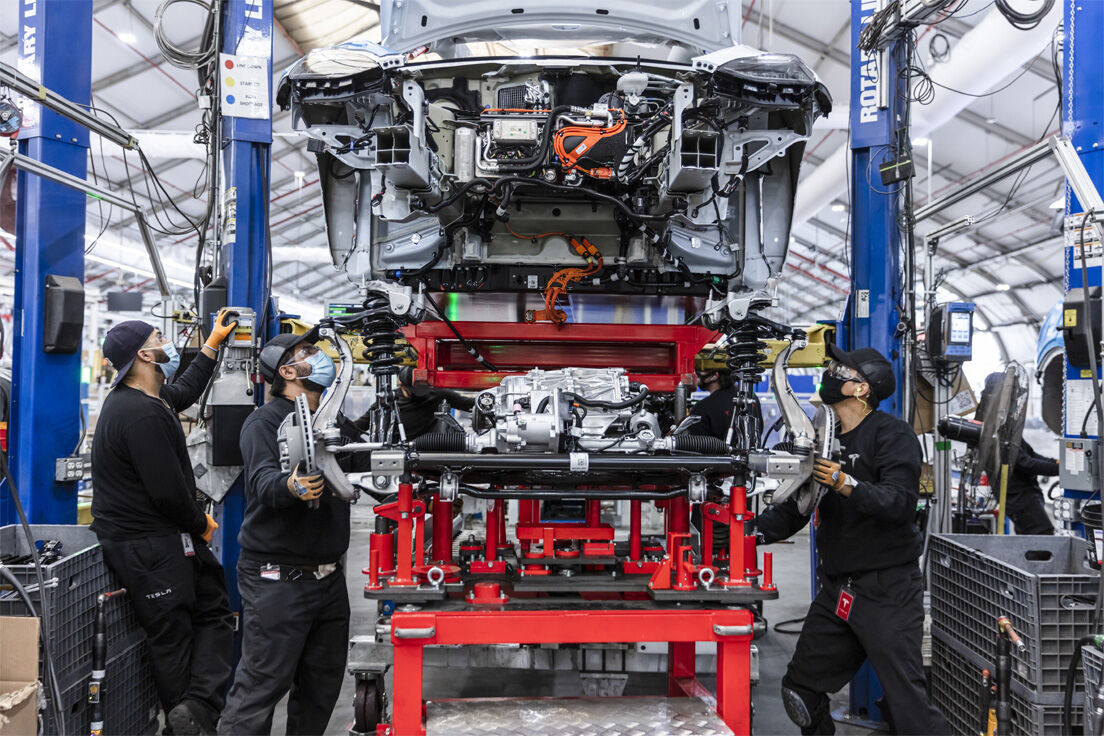
Furthermore, Tesla leverages the pliability of 3D printing with sand to experiment with intricate designs beforehand thought-about too dangerous or costly. As an illustration, Tesla’s engineers can now embrace hole subframes of their one-piece castings to cut back weight and enhance crashworthiness. Engineers place 3D printed sand cores inside the molds to create these hole buildings. After casting the steel, they take away the sand, leaving the specified hole areas behind.
Mould magic
Tesla prefers in-house options and tends to be secretive about its manufacturing strategies. Regardless of this, the corporate has embraced 3D printing for numerous functions. A Forbes report revealed that Tesla’s purposes of this know-how vary from creating door handles to prototyping whole chassis. For Tesla’s particular have to create 3D printed sand molds, binder jetting know-how could be the go-to methodology. These printers depend on layering, spreading sand on a tray, after which selectively making use of a liquid binder to form the mould in response to the digital design. The machine repeats the method layer by layer to finish the mould after which removes the unbound sand to disclose the completed product.
In keeping with one Reuter supply, the price of “the design validation course of with sand casting, even with a number of variations, is minimal – simply 3% of doing the identical with a steel prototype.”
Whereas Tesla has been exploring this know-how, different gamers within the business, resembling BMW and Cadillac (for its ultra-luxury EV CELESTIQ), have already embraced binder jetting for his or her purposes. Apparently, they’ve teamed up with voxeljet (Nasdaq: VJET), which uniquely presents sand printers giant sufficient for such large-scale purposes. Though different firms like Desktop Steel (NYSE: DM) and its lately acquired ExOne additionally provide binder jetting machines tailor-made for one of these software, Tesla may observe the steps of opponents. It’s price noting that voxeljet presently faces some monetary challenges, with a market cap of simply $10 million, lower than a 12 months of money runway, declining earnings over the previous 5 years, and up to date share value volatility. Given Tesla’s inclination for in-house options and voxeljet’s specialised capabilities, Tesla’s acquisition of voxeljet printers may present monetary stability to the 3D printing model.
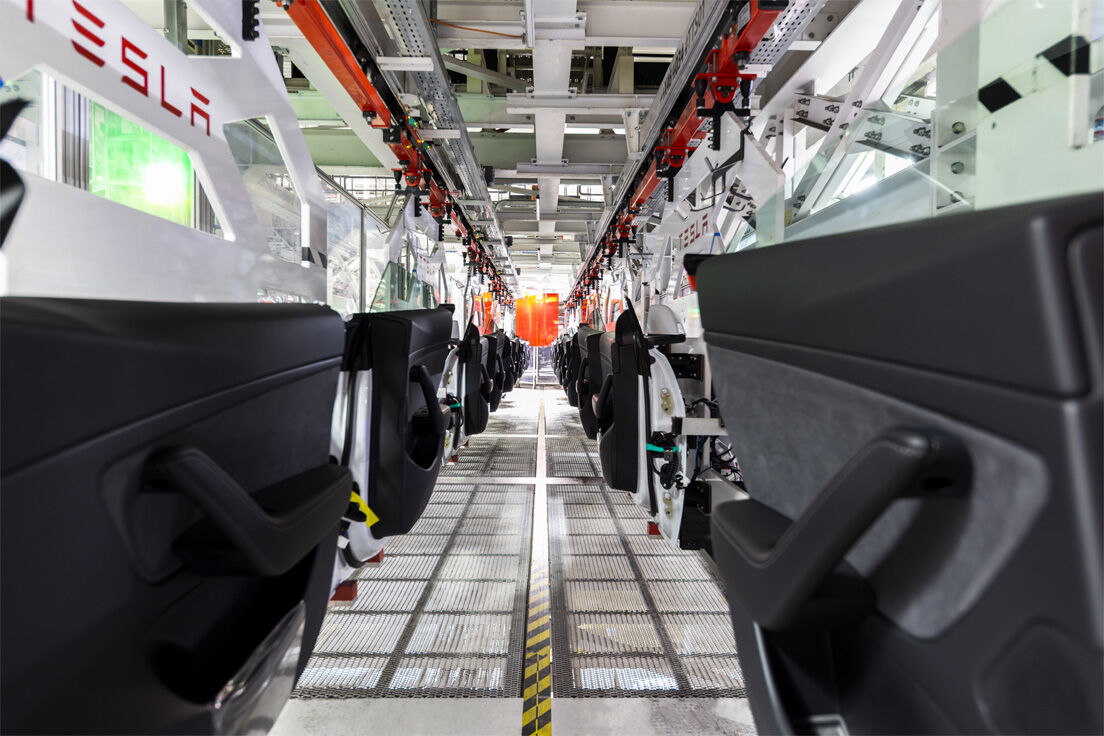
Earlier this 12 months, CEO Elon Musk unveiled Tesla’s bigger “unboxed” manufacturing technique, which aligns with the corporate’s choice to make use of 3D printed sand molds. The strategy goals to streamline manufacturing by creating giant automobile sub-assemblies, snapping them collectively like constructing blocks. By mastering the artwork of casting giant, complicated buildings in a single piece, Tesla not solely simplifies the manufacturing course of but additionally stands to cut back manufacturing prices considerably.
Price cutter
Tesla has been a disruptive power within the automotive business since its inception, revolutionizing a number of sides of EVs. From pioneering long-lasting lithium-ion batteries to growing a proprietary community of fast-charging stations, Tesla has constantly damaged down obstacles to EV adoption. Not like conventional automakers, Tesla additionally launched over-the-air software program updates, enabling real-time enhancements with out requiring a visit to the service heart.
Moreover, Tesla’s groundbreaking large Gigafactories have scaled up battery manufacturing to unprecedented ranges, considerably decreasing the price of batteries for EVs. This can be a departure from conventional manufacturing, which frequently lacks the size and integration to drive down battery prices successfully. As well as, Tesla employs extremely automated meeting traces, contrasting with the much less automated and extra labor-intensive processes generally present in conventional manufacturing. These meeting traces use robotics and superior software program for elevated precision. Tesla additionally engages in in-house part manufacturing, giving them larger management over the standard and effectivity of the manufacturing course of, a distinction to the reliance on exterior suppliers typical of conventional automakers.
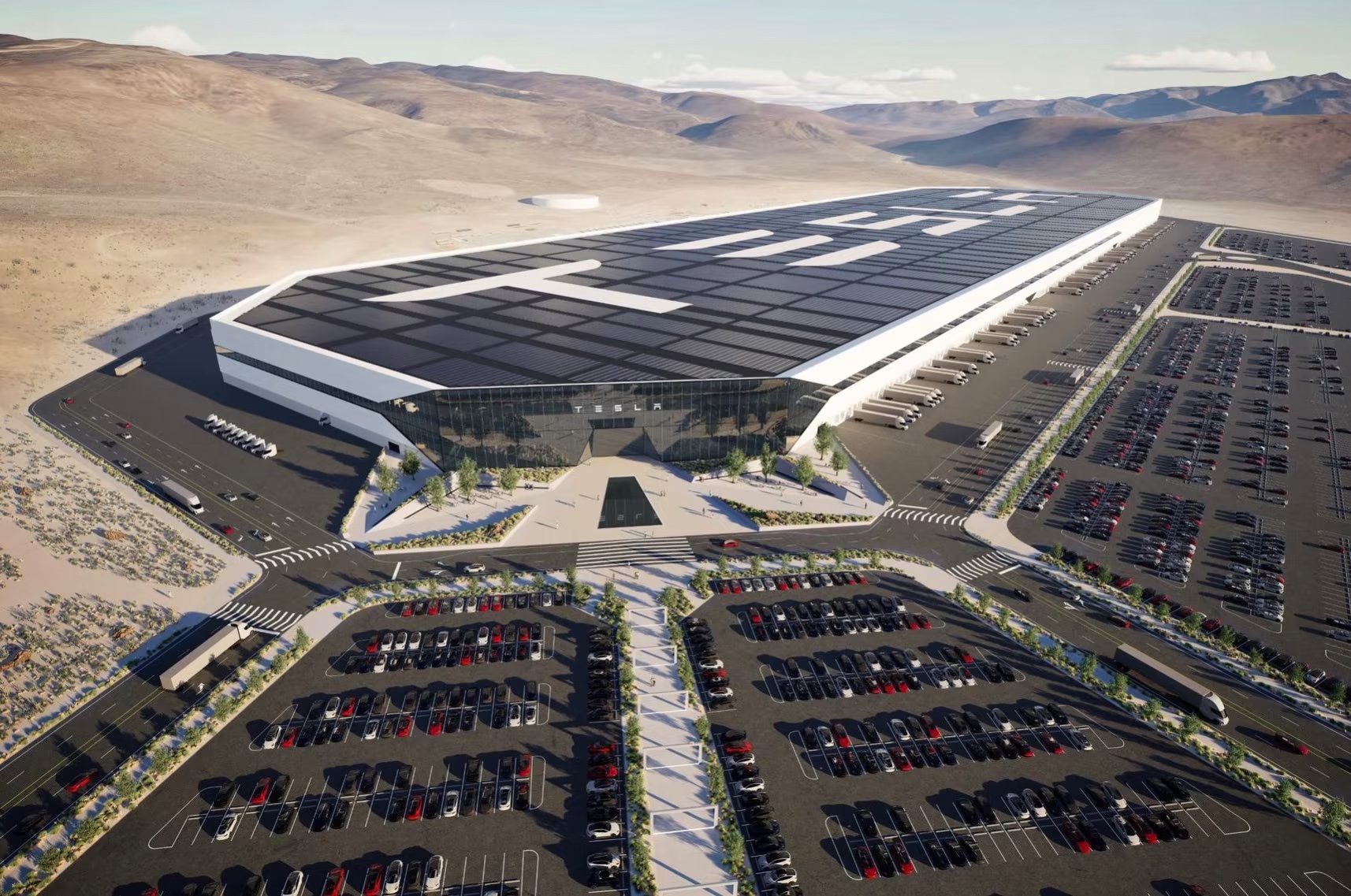
If profitable, implementing 3D printing know-how for sand molding represents only one aspect of Tesla’s multi-pronged technique to revolutionize the automotive business. Nevertheless, its potential influence might be huge as a catalyst for accelerated EV manufacturing and a benchmark for future manufacturing innovation. If Tesla succeeds, it is not going to solely fulfill its aim of manufacturing cheaper and extra accessible electrical automobiles however may set a brand new normal for automobile manufacturing worldwide.
Subscribe to Our E-mail Publication
Keep up-to-date on all the most recent information from the 3D printing business and obtain info and presents from third celebration distributors.