In 2022, Thai an organization by the identify of “The Concrete Merchandise and Mixture Co., Ltd” (an affiliate of Siam Cement Group) efficiently constructed the world’s first 2-story residential PPVC constructing in Saraburi, Thailand. It was constructed utilizing 3D printed prefabricated prefinished volumetric development (PPVC) expertise, and resulted in a constructing masking a complete space of 68 sq. meters.
Let’s check out the mission, named “CPAC-PP3DVC” in some extra element.
CPAC-PP3DVC
Prefabricated Prefinished Volumetric Development (PPVC) is a development methodology whereby free-standing three dimensional modules are accomplished with inside finishes, fixtures and fittings in an off-site fabrication facility, earlier than it’s delivered and put in on-site.
Utilizing the PPVC methodology of development has quite a few benefits together with elevated productiveness, a greater development surroundings (free from publicity to the weather, and mud), and improved high quality.
Usually PPVC buildings are made off-site utilizing molds and poured concrete – PP3DVC does away with the molds, and as a substitute makes use of 3D development printing to realize the identical objectives of modular development.
And that is precisely what The Concrete Merchandise and Mixture Co (often known as “CPAC”) has used to realize their world-first development in Saraburi. You possibly can see the assembled constructing at its last location within the picture beneath.
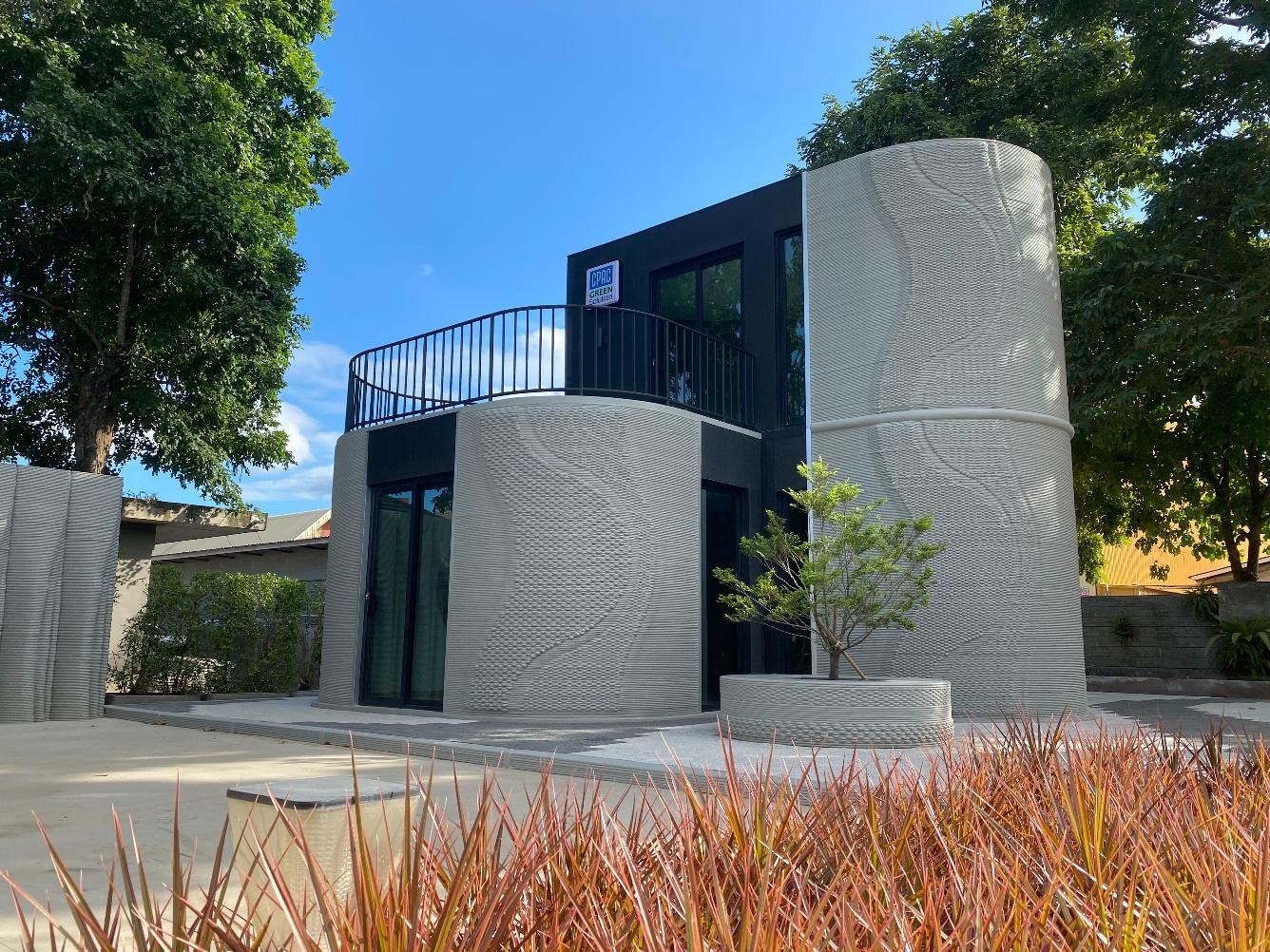
Comprising 4 modules of various dimensions (starting from 3×3 meters to three×6 meters), every module was 3D printed to characteristic distinctive curved partitions, adorned with numerous parametrically-designed textures. The digital design of the modules was carried out to make sure that every module had the optimum wall thermal properties.
The constructing’s structural integrity combines the energy of 3D printed mortar partitions with a metal body. A rigorous finite ingredient evaluation was performed to make sure security all through the constructing’s lifecycle, from development and transportation, to when the constructing is in use.
Light-weight Development for Effectivity
Modular development usually grapples with the burden of modules, posing challenges throughout meeting. In a bid to mitigate these issues, the CPAC-PP3DVC mission imposed a most module weight restrict of 10 tons, considerably lighter than conventional bolstered concrete modules.
To perform this feat, engineers developed a light-weight 3D printing mortar with a density of 1,600 kg/m³, rendering it 16% lighter than standard counterparts. Remarkably, this light-weight mortar boasted comparable compressive energy, guaranteeing the constructing’s robustness.
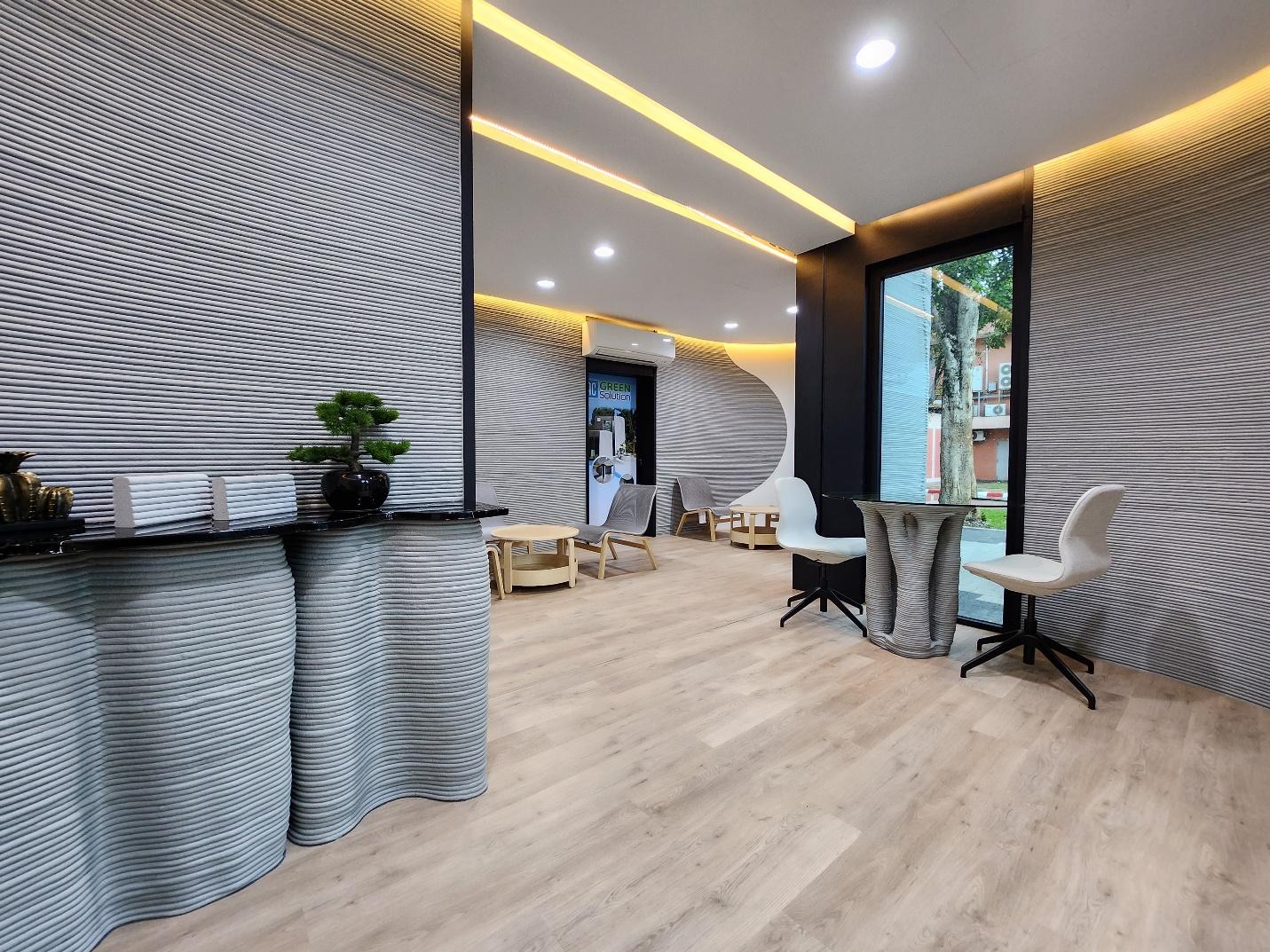
The constructing’s flooring system additionally adopted an revolutionary method, embracing a hybrid steel-concrete composite system to scale back flooring weight by 40% in comparison with conventional strategies. Collaborative analysis between SCG and universities optimized the 3D printed partitions to include infill concrete with reinforcement, reaching superior wall design efficiency. Finally, the 3D printed PPVC modules weighed in at a formidable 70% lower than their bolstered concrete counterparts.
Off-Web site Ending and Fast Meeting
Embracing the PPVC methodology, the CPAC-PP3DVC constructing was accomplished with inside finishes, fixtures, and fittings at an off-site fabrication facility earlier than being transported to the development website. This dramatically elevated development productiveness and minimized reliance on on-site labor. To additional speed up development, 3D printed footing formwork was employed.
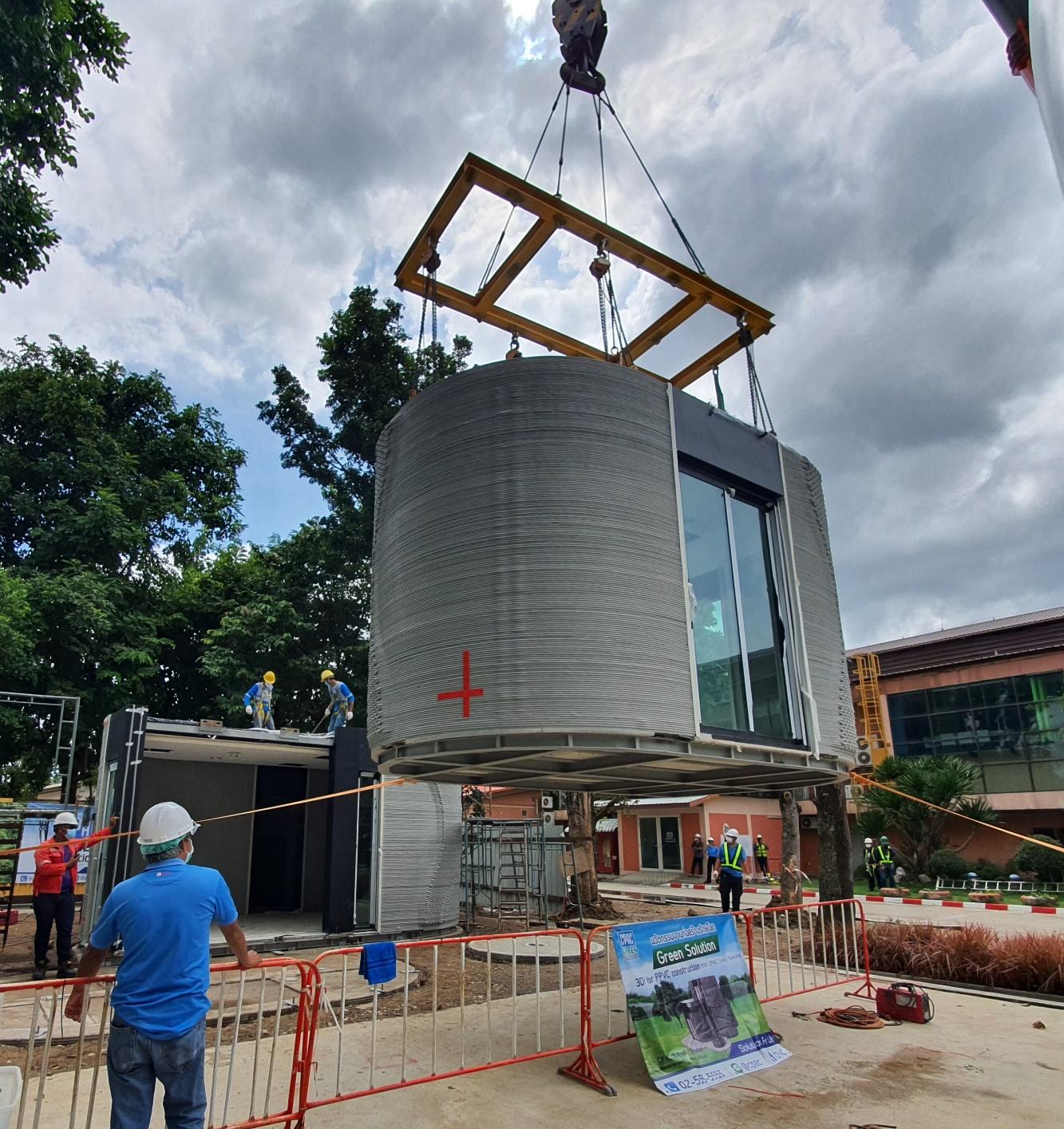
One of the spectacular feats of the CPAC-PP3DVC mission was its speedy meeting. Your entire constructing was erected in simply 4 hours, and the mission’s development timeline was accomplished in roughly eight weeks, 51% quicker than conventional brick-and-mortar development strategies.
Sustainability and Lowered Waste
Past the spectacular development velocity, the CPAC-PP3DVC constructing additionally demonstrated sustainable development practices, with the 3D printed PPVC method leading to a staggering 95% discount in development waste in comparison with masonry development strategies.
This equated to a discount of three.7 tons of CO2 equal when it comes to waste supplies. Sustainability metrics like this reveal that PP3DVC development strategies could make a major contribution to the battle towards local weather change.
Conclusion
All-in-all, the CPAC-PP3DVC has proven that 3D printing of buildings has nice promise, particularly when contractors don’t have to move development printers and supplies to a website. The pre-fabrication of the modules with 3D printers allowed the designers and engineers to provide buildings as sturdy as historically fashioned PPVC buildings, with the added benefits of lowered CO2 footprint, and mold-free textured finishes.
The constructing is now operational, and serves as a co-working house for the local people.
CPAC will probably be presenting their mission on the sixteenth Worldwide Congress on the Chemistry of Cement 2023, which will probably be held on the Centara Grand & Bangkok Conference Centre At Centralworld, Bangkok, on 18-22 September 2023. So if you’re within the Bangkok space and want to study extra about PP3DVC development, then head on over to the congress to seek out out extra.
Come and tell us your ideas on our Fb, Twitter, and LinkedIn pages, and don’t overlook to enroll in our weekly additive manufacturing e-newsletter to get all the newest tales delivered proper to your inbox.