Kicking off at the moment’s 3D Printing Information Briefs, Eplus3D launched a brand new hybrid manufacturing answer. In supplies information, Formlabs has launched its first versatile SLS 3D printing materials. Then it’s on to dental and medical functions, as Carbon introduced a brand new manufacturing choice for 3D printed clear aligners and QUT researchers are investigating 3D printing insoles for folks in distant areas with diabetes-related foot illness. Lastly, a global design studio has revealed its plan for a 3D printed, climate-responsive pavilion.
Eplus3D Introduces MPBF Hybrid Manufacturing Resolution
Metallic additive manufacturing options supplier Eplus3d just lately launched its new MPBF Hybrid Manufacturing Resolution, meant to enhance hybrid manufacturing of metallic 3D printing. The answer is used for automated hybrid manufacturing, and options one-click positioning—the software program collects photographs, and obtains the contour map, of the elements, then makes use of these to robotically calculate their place data. Customers solely want a fundamental understanding powder-based AM processes to make use of this new workflow, which boosts the accuracy and effectivity of the 3D printed elements, in addition to improves metallic AM competitiveness and lowers manufacturing prices.
The consumer will information the software program to acknowledge each the internal and outer contours of an element on the machine’s working display. Then, the software program will robotically place the info with, as Eplus3D says, “a reposition accuracy of decrease than 0.1mm.” The system makes use of the identical digital camera because the one within the firm’s lively powder mattress monitoring module, so it’s straightforward to combine this answer for purchasers already utilizing the monitoring operate. The brand new MPBF Hybrid Manufacturing Resolution efficiently accomplished testing, and received acceptance from Eplus3D’s lead prospects, and all prospects are actually eligible to improve their present methods with this Hybrid Module. The answer will doubtless be used within the automotive and tooling industries, particularly for mold-making functions.
Formlabs Declares First Versatile SLS Materials
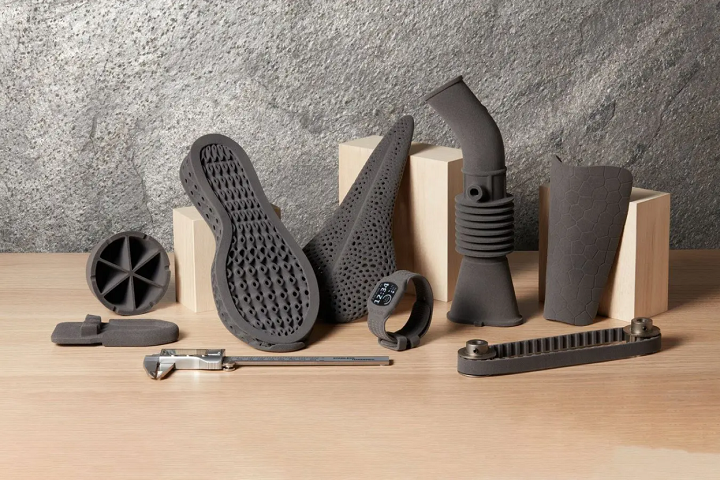
TPU 90A Powder is right for prototyping practical prototypes for elements that require flexibility, like skin-safe wearables, efficiency sports activities gear, or shoe insoles.
Formlabs has launched its first soft-touch materials for the Fuse Sequence SLS 3D printers: TPU 90A powder, a versatile elastomer with functions in protecting sporting gear, skin-safe wearables, manufacturing aids like gaskets, seals, and plugs, and medical units like splints, orthotics, and prosthetics. The sturdy, rubbery materials is nice for printing quick, versatile, and geometrically superior elements in-house, and options the corporate’s lowest refresh charge—20%—of all of its SLS powders, which helps scale back price per half. Formlabs says with TPU 90A and its Fuse Sequence, it’s now doable to constantly 3D print soft-touch elements that had been beforehand mass-produced for reliability. Customers can simply combine the powder right into a Fuse Sequence and Fuse Sift workflow, as the fabric doesn’t require an inert ambiance, and the depowdering course of is pretty easy, as TPU elements don’t use Floor Armor. One buyer that’s very pleased with utilizing TPU 90A for practical prototyping is Radio Flyer, the maker of the long-lasting Unique Little Crimson Wagon®.
“The high-grip floor end is exclusive in comparison with different 3D printed TPE/TPUs I’ve interacted with. From that standpoint, it does really feel extra just like our injection molded TPE/TPU which is thrilling from a prototype software. At present, the following greatest various to this course of could be a prototype instrument and injecting precise TPE or different urethanes so that is each extra price and time efficient,” mentioned Radio Flyer’s improvement course of, and design engineer Agostino Lobello.
“The elements themselves look like fairly sturdy. We might don’t have any points putting in them on works-like prototypes and sending them dwelling for testing for ergonomic and value suggestions. We’re excited concerning the prospect of utilizing this materials for tire treads, hand grips, bumpers, seat cushions, and as a solution to prototype TPE springs with a particular spring-rate.”
Carbon’s Gen 2 Aligner Mannequin 3D Printing Resolution Boosts Effectivity
On the latest Worldwide Dental Present in Cologne, Carbon introduced a new sustainable 3D printing answer for extra environment friendly clear aligner mannequin manufacturing. The Carbon Gen 2 aligner mannequin answer is claimed to supply vital price financial savings, in addition to a 65% improve in throughput and fewer materials per print. The answer integrates with the corporate’s present 3D printer {hardware} and aligner mannequin workflow, and is made up of the Carbon L1 3D printer, new UMA 20 high-performance resin, solventless spin cleansing answer, and new proprietary API-based software program that automates mannequin hollowing, nesting, and batching. The brand new Carbon Gen 2 aligner mannequin answer can be obtainable to prospects later this 12 months.
“Working with the highest clear aligner firms has given us perception into the boundaries this trade faces every day. We heard from prospects and we took motion to create efficiencies and value financial savings within the clear aligner workflow. This new aligner workflow is designed to allow Carbon prospects scale back price per half whereas concurrently bettering mannequin throughput with a extra sustainable manufacturing course of,” mentioned Terri Capriolo, Senior Vice President, Oral Well being at Carbon.
QUT Researchers Obtain Grant for 3D Printed Diabetic Insoles Mission
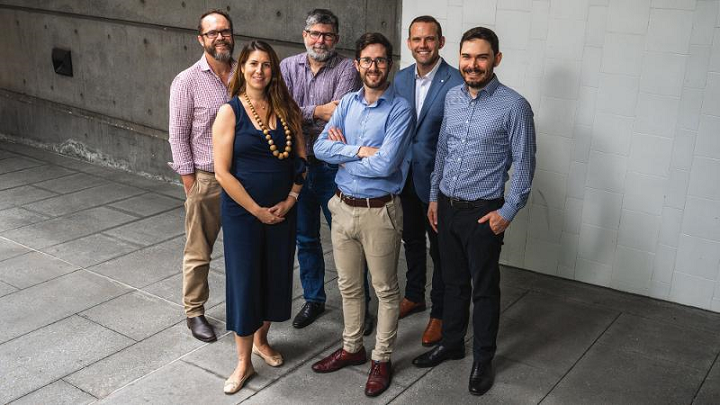
Pictured from again left: QUT’s Affiliate Professor Peter Lazzarini, Professor Mia Woodruff, Dr Sean Powell, Dr Edmund Pickering, Affiliate Professor David Holmes, Alex Terrill
A staff of researchers from Queensland College of Know-how (QUT) has been engaged on a mission to 3D print customized, low-cost, pressure-offloading insoles for folks in distant areas dwelling with diabetes-related foot illness. Folks in distant or regional areas can have much less entry to podiatry providers, which ends up in lowered possibilities of their diabetes-related foot ulcers therapeutic; finally, this contributes to the next danger of amputation. The mission, “3D digital options for diabetes-related foot ulcer offload therapy,” just lately acquired a $810,000 Medical Analysis Future Fund Main Well being Care Digital Improvements Grant to assist with their work. The trade accomplice is Aptium3D, whereas different members of the analysis staff embody Professor Jonathan Golledge from James Cook dinner College and Dr Kerrie Evans from the College of Sydney, in addition to affiliate investigators Dean Hartley, Chief Know-how Officer, Healthia Ltd, and Scott Morrison, Normal Supervisor, iOrthotics, Higher Brisbane.
“Our analysis staff will develop and consider low-cost foot scanning applied sciences, developed in partnership with Aptium3D inside a longtime digital framework,” mentioned Professor Mia Woodruff, from the QUT Centre for Biomedical Applied sciences.
“These applied sciences can be built-in within the allied healthcare organisation, Healthia’s, diabetes-related foot ulcer (DFU) monitoring, prognosis and therapy pipeline to be used in regional communities.
“Our modern 3D dynamic foot scanner can be utilized by skilled podiatrists as a telehealth machine for distant monitoring and prognosis.
“It will likely be coupled with superior, versatile, metamaterial 3D-printing applied sciences to create personalised insoles to assist shield the toes from harm and ulceration.”
3D Printed Local weather-Responsive Public Pavilion
As we cope with the worldwide disaster of plastic waste, worldwide design studio Hassell is working with to.org and Nagami, a 3D printing design studio, to develop a public pavilion 3D printed from recycled plastic, which could possibly be shortly tailored to suit a wide range of environments. Impressed by indigenous shelters and meant to function a gathering place for schooling and meditation, this proof of idea pavilion was created utilizing computational approaches, can run off the grid with minimal power, and is completely 3D printed, which makes it cheaper to adapt the shelter. The principle construction can be printed in 24 separate items, so it may be simply transported and assembled onsite, and is climate-sensitive; as an example, it will likely be hermetically closed within the chilly, with fins on its outer pores and skin designed to seize snow for pure insulation. Throughout hotter climates, overlapping fins will enable for cross air flow, passive cooling, and water harvesting.
“We’ve greater than 5 billion metric tons of plastic waste on our planet. As 3D printing scales up into the area of structure and development, we are able to massively improve the demand for recycled plastics, and subsequently pace up the cleansing technique of our oceans and landfills,” mentioned Manuel Jimenez Garcia, Founding father of Nagami. “We hope this mission will contribute to inspiring a brand new era of architects to really consider {that a} radical change in development, pushed by eco-innovation, is really doable.”
Subscribe to Our E-mail E-newsletter
Keep up-to-date on all the most recent information from the 3D printing trade and obtain data and affords from third get together distributors.