PTC has lately showcased a groundbreaking achievement in additive manufacturing on the LiveWorx 2023 occasion. They unveiled a “totally additively manufactured jet engine”, weighing round 3.6 kg, which was designed utilizing PTC’s Creo CAD software program.
The undertaking was spearheaded by Dr. Ronen Ben Horin, Vice President of Know-how at PTC and Senior Analysis Fellow at Technion – Israel Institute of Know-how, together with Beni Cukurel, an Affiliate Professor of Aerospace at Technion. Their aim was to create a self-supported micro turbojet engine that required no meeting, together with all rotating and stationary elements, representing a big breakthrough in designing for Additive Manufacturing (DfAM).
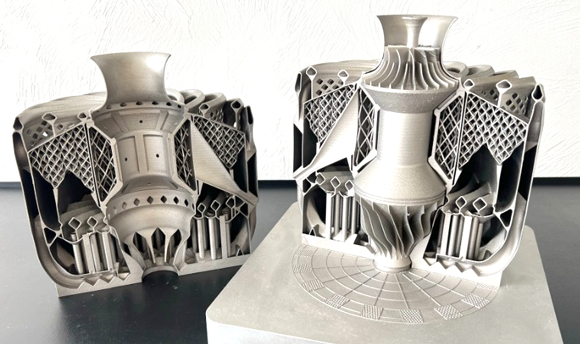
PTC’s Creo software program performed an important position within the design course of, leveraging its superior capabilities for lattice modeling and generative design. This allowed for materials and weight discount whereas sustaining the engine’s power and efficiency. Creo’s beam-based lattices robotically optimized designs for additive manufacturing, and the software program supported self-supported formula-driven lattices, which may very well be adjusted for manufacturing effectivity.
Moreover, Creo was appropriate with numerous additive manufacturing gear, facilitating the construct and post-processing levels. The software program’s 3D part design capabilities additionally enabled conventional machining for exact meeting. Moreover, Creo provided a spread of codecs, together with 3MF, for sending 3D fashions to totally different printer applied sciences available in the market.
PTC’s totally additively manufactured jet engine represents a outstanding achievement within the area of additive manufacturing, demonstrating the ability of superior design software program like Creo in pushing the boundaries of what’s potential on this area. This breakthrough opens up new prospects for light-weight and high-performance engine designs, with potential functions in aviation and different industries.
Come and tell us your ideas on our Fb, Twitter, and LinkedIn pages, and don’t overlook to join our weekly additive manufacturing e-newsletter to get all the most recent tales delivered proper to your inbox.